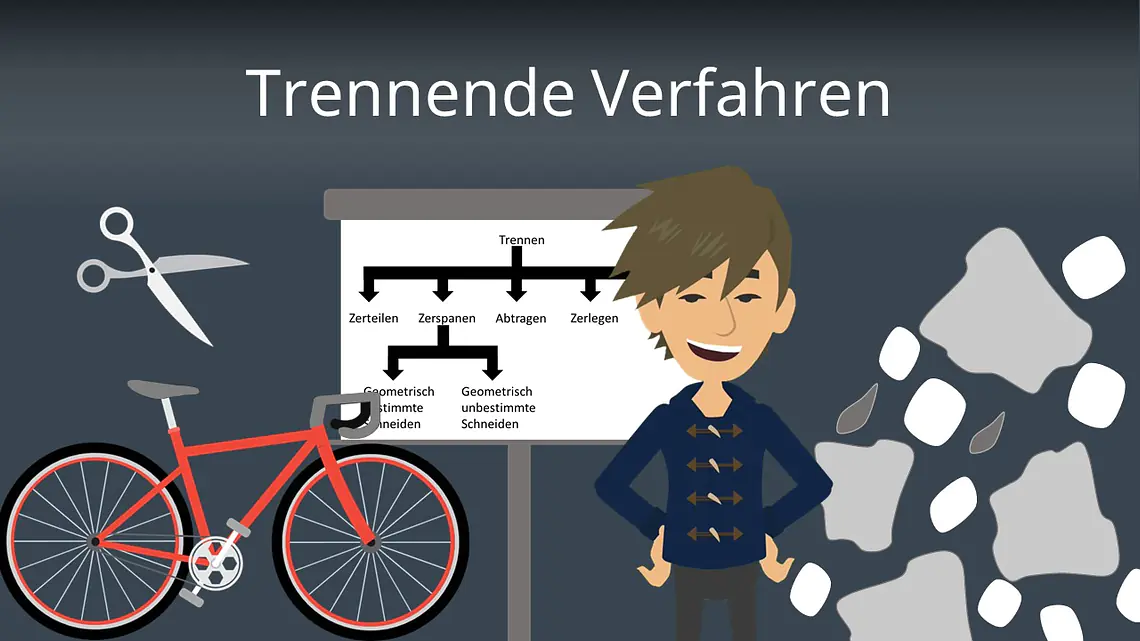
Trennende Verfahren
Du hörst das Wort „trennen“ und denkst sofort an ein gebrochenes Herz, Tränen und Unmengen an Schokolade? Nach diesem Video sicherlich nicht mehr!
Inhaltsübersicht
Die sechs Kategorien
In der Fertigungstechnik wird auch getrennt – allerdings ohne Tränen und Drama. Trennende Verfahren bilden die dritte Hauptgruppe. Genauer unterteilt sich diese Gruppe in sechs weitere Kategorien: Zerteilen, Zerspanen mit geometrisch bestimmten oder unbestimmten Schneiden, Abtragen, Zerlegen und Reinigen. Sehen wir uns zunächst einmal das Zerteilen an.
Das Zerteilen
Das wichtigste und bekannteste Verfahren beim Zerteilen kennst du bestimmt schon. Bewegen sich zwei Schneiden aneinander vorbei und trennen das Werkstück, spricht man vom Scherschneiden. Das kennst du also bereits von klein auf durch die Haushaltsschere. Bei zerteilenden Verfahren entstehen keine formlosen Stoffe wie Späne oder Pulver als Nebenprodukt.
Das Zerspanen
Wenn man hingegen von Zerspanen spricht, wird ein Werkstück so bearbeitet, dass Teile vom Werkstück entfernt werden und diese Nebenprodukte entstehen. Die Gruppe der Verfahren, die dabei mit geometrisch bestimmten Schneiden arbeitet, beinhaltet zum Beispiel das Drehen, Bohren, Fräsen und Sägen. Sie zeichnen sich alle dadurch aus, dass die Hauptbewegung rotatorisch abläuft. Beim Drehen ist es allerdings nicht das Werkzeug, das sich dreht, sondern das Werkstück. So lässt sich gleichmäßig etwas vom Durchmesser abtragen und es entstehen saubere Übergänge.
In der Industrie gibt es für das Drehen sogenannte CNC- Universaldrehmaschinen, die verschiedene Drehvorgänge umsetzen können. CNC steht für computerized numerical control. Das Besondere ist, dass sie nicht nur vollautomatisch arbeiten, sondern auch in der Lage sind Programme abzuspeichern.
Das Fräsen
Unter den Fräsen werden am häufigsten Umfangs- und Stirnfräsen eingesetzt. Eine Umfangsfräse findet ihren Einsatz, wenn besonders viel vom Werkstück abgetragen werden soll. Bei der Stirnfräse kannst Du dir anhand ihrer horizontalen Position zur Oberfläche des Werkstücks bestimmt schon vorstellen, dass sie sich besonders gut zum Bearbeiten von Konturen und Flächen eignet. Auch mit einer translatorischen Hauptbewegung lässt sich spanen; das ist aber eher selten. Diese Verfahren heißen Räumen, Hobeln und Stoßen.
Das Schleifen
Da wir uns in diesem Video nur einen groben Überblick verschaffen möchten, kommen wir nun zum Schleifen, dem wichtigsten Verfahren der Kategorie Spanen mit geometrisch unbestimmten Schneiden. Bestimmt hast du schon einmal einen Fahrradrahmen abgeschliffen oder eine Holzplatte mit Schleifpapier bearbeitet. Vergleichst Du das Schleifen mit Sägen oder Bohren, so ist es eher ein Verfahren zur Feinbearbeitung von Werkstücken.
Siehst du dir ein Schleifwerkzeug einmal genauer an, so erkennst du Schleifkörner, die an manchen Stellen miteinander verbunden sind. Neben den Bindungen existieren sogenannte Poren oder Spanräume. Beim Schleifen bewegt sich das Schleifwerkzeug nun entgegengesetzt zum Werkstück und trägt durch die Außenkontur der Schleifkörner kleine Späne ab. Je feiner die Körner des Schleifmaterials sind, desto höher ist die Oberflächengüte des Werkstücks. Um Keramiken, Hartmetall oder auch Verbundwerkstoffe wie Glasfaserverstärkte Kunststoffe zu bearbeiten, verwendet man Diamantkörner zum Schleifen. Das eher weiche Aluminium hingegen wird meistens mit Siliziumkarbid, einer Verbindung aus Kohlenstoff und Silizium, geschliffen.
Je nachdem welche Zielvorgaben wie Oberflächengüte, Form- und Maßgenauigkeit aber auch Fertigungskosten das Werkstück haben soll, kommen verschiedene Schleifvarianten zum Einsatz. Die Hauptunterteilungen erfolgen in Rund- und Flachschleifen sowie Seiten- und Umfangsschleifen. Das Flachschleifen wird zum Beispiel zur Bearbeitung von Turbinenschaufeln oder Heckenscheren eingesetzt. Jetzt hast Du die wichtigsten Begriffe der trennenden Verfahren kennengelernt!
Nachdem du jetzt weißt, was Trennen ohne Herzschmerz bedeutet, kannst Du dich gleich zu den Laser- und Wasserstrahlverfahren weiterklicken!