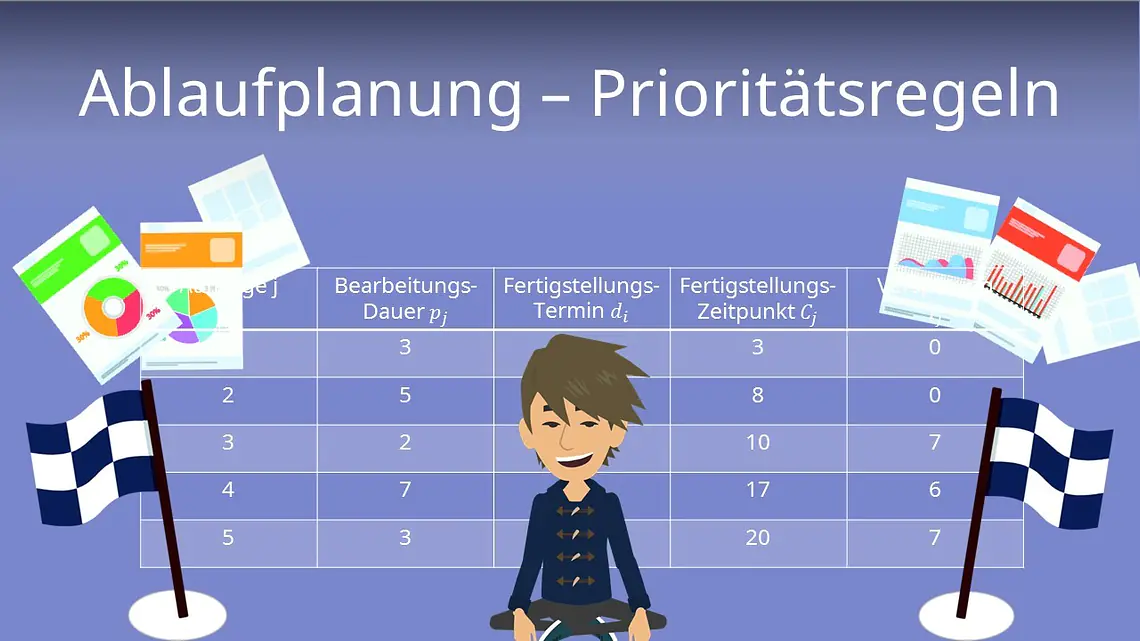
Prioritätsregeln der Ablaufplanung
Du hast keine Ahnung was die Prioritätsregeln in der Ablaufplanung sind? Das ändern wir jetzt!
Wenn du das Thema noch schneller verstehen möchtest, dann schau dir direkt unser Video an.
Inhaltsübersicht
Ablaufplanung bzw. Maschinenbelegungsplanung
Bei der Ablaufplanung geht es darum den Maschinen Produktionsaufträge zuzuordnen und eine Reihenfolge zu bestimmen. Deswegen wird sie auch als Maschinenbelegungsplanung bezeichnet. Dabei müssen unter Umständen zusätzliche Bedingungen berücksichtigt werden, z.B. kann auf deine Uhr erst dann das Glas aufgesetzt werden, wenn das Uhrwerk schon eingebaut ist. Also muss das Uhrwerk auch vor dem Glas fertig sein. Eigentlich logisch oder?
Es gibt verschiedene Möglichkeiten die Ablaufplanung zu gestalten. Welche Variante am besten ist, hängt von deinem Ziel ab. In diesem Video schauen wir uns die verschiedenen Prioritätsregelverfahren an. Solltest du Fragen zur Ablaufplanung des Moores – und Johnson-Algorithmus oder zu Job-shop haben, dann schau dir unsere Videos dazu an.
Operationale Ziele
Es gibt verschiedene Ziele in der Ablaufplanung, die manchmal auch in Konkurrenz zueinanderstehen. Sie lassen sich in vier Überpunkte unterteilen: Die Kapazitätsauslastung, die Bestände, den Lieferservice und die Handhabung von Belastungsspitzen beziehungsweise Überstunden. Damit es leichter für dich ist, die verschiedenen Ziele zu verfolgen, gibt es die operationalen Ziele der Ablaufplanung. Operational bedeutet, dass sich die Ziele auf den Produktionsprozess beziehen. Sie sind also quasi die Hilfsziele für die eigentlichen Ziele.
Wenn dein Ziel beispielsweise ein guter Lieferservice ist, dann lässt sich anhand dieser Vorgabe schwer etwas verbessern. Wenn du konkrete Vorgaben erfüllt haben möchtest, musst du schon etwas genauer werden. Dir ist zum Beispiel die Pünktlichkeit deiner Lieferungen wichtig? Dann sieht das operationale Ziele so aus: Minimiere die Anzahl verspäteter Aufträge. Diese Zielvorgabe lässt sich dann auch praktisch umsetzten. Operationale Ziele können durchlaufzeitbezogen, terminorientiert oder kapazitätsorientiert sein.
Die verschiedenen Prioritätsregelverfahren bestehen grundsätzlich aus zwei Schritten: Zunächst werden die Aufträge priorisiert und entsprechend ihrer Priorität sortiert. Dann werden die Aufträge entsprechend der erstellten Reihenfolge den Maschinen zugeordnet und terminiert. Diesen Vorgang nennt man Allokation.
Prioritätsregelverfahren Beispiel
Wir schauen uns das Vorgehen an einem Beispiel an.
Du hast fünf Aufträge j für verschiedene Uhren, die du produzieren sollst. Zusätzlich ist eine Bearbeitungsdauer p von j gleich 3,5,2,7,3 und der späteste Fertigstellungstermin d von i gleich 7,10,3,11,13 gegeben. Je nachdem, welches Prioritätsregelverfahren du anwendest, werden die Aufträge unterschiedlich angeordnet. Um die Werte der Prioritätsregeln vergleichbar zu machen, bestimmen wir immer jeweils die Anzahl der Verspätungen t#, die größte Verspätung t max und den durchschnittlichen Fertigstellungszeitpunkt F average – kurz F ave.
First Come First Serve Regel
Das wohl bekannteste Verfahren ist die First Come First Serve Regel. Sie wird häufig als Maßstab zum Vergleich der verschiedenen Prioritätsregeln verwendet.
Bei der FCFS-Regel werden die Aufträge gemäß ihrer Auftragsnummer bearbeitet. Erst Auftrag 1, dann Auftrag 2 usw.. Schauen wir uns das anhand unseres Beispiels an. Die Dauer und der späteste Fertigstellungszeitpunkt eines Auftrages bleiben immer gleich. Der Fertigstellungszeitpunkt C von j verändert sich allerdings. Er wird durch die Summe der Dauer der bisherigen Aufträge bestimmt. Der jeweilige Fertigstellungszeitpunkt z.B. von C von 5 gleich 20 wird dann mit dem zugehörigen Fertigstellungstermin, also mit d von 5 gleich 13 verglichen. Ist C von J kleiner gleich d von i dann ist die Verspätung null. Ist C von J größer als d von i, dann gibt es eine Verspätung in Höhe der Differenz der beiden. In unserem Beispiel also 20- 13 = 7
Shortest Processing Time-Regel und Earliest Due Date Regel
Jetzt möchten wir noch die Werte F ave, t max und t Raute für die FCFS-Regel herausfinden.
F ave ermitteln wir, indem wir die Summe aller Fertigstellungszeitpunkte durch die Anzahl der Aufträge teilen:
Die größte Verspätung t max kannst du in der letzten Spalte ablesen, sie ist in unserem Beispiel 7. Diese Spalte brauchen wir auch für die Anzahl der Verspätungen t Raute. Wir zählen die Anzahl der Aufträge, die verspätet sind, zusammen und kommen auf einen Wert von 3.
Kommen wir zur Shortest Processing Time-Regel. Hier werden die Aufträge nach der Durchlaufzeit aufsteigend sortiert.
Die Auftragsreihenfolge ist jetzt 3,1,5,2,4 und die daraus resultierenden Fertigstellungszeitpunkte 2,5,8,13,20. Damit liegen die Verspätungen bei 0,0,0,3,9
F ave ergibt sich hier zu:
t max ist 9 und t Raute gleich 2.
Wie du in diesem Beispiel sehen kannst, sorgt die SPT-Regel dafür, dass die mittlere Durchlaufzeit minimiert wird. Wenn du also möglichst viel Uhren, möglichst schnell produzieren willst, solltest du dich für die SPT-Regel entscheiden. Es kann allerdings auch nach Longest Processing Time sortiert werden, dann kommen zuerst die Aufträge an die Reihe, die eine lange Bearbeitungszeit haben. Die Anwendung der LPT-Regel sorgt dafür, dass die Aufträge am Ende deutlich schneller fertig werden.
Als nächstes ist die Earliest Due Date Regel an der Reihe. Dabei kommt immer der Auftrag als nächstes, der am frühesten fertig gestellt sein muss.
Die neue Reihenfolge ist 3,1,2,4,5 mit den Fertigstellungszeitpunkten 2,5,10,17,20 und der jeweiligen Verspätung 0,0,0,6,7.
F ave = , t max = 7 und t#= 2. In diesem Beispiel ist es schon ein wenig zu erkennen: die EDD-Regel minimiert die maximale Verspätung.
So das war`s auch schon wieder von den Prioritätsregeln. Jetzt weißt du, welches Verfahren du für welches Ziel anwenden musst.